It’s the time of year for predictions. It’s a time of change in manufacturing globally. Closer to home, the China Australia FTA will affect competitiveness. So here are our thoughts on manufacturing trends for 2015 and beyond. And of course we focus on the markets we know best – Australia and China.
Here are the most talked about manufacturing trends, with our opinions:
1. 3D Printing
We wrote about this back in April, when the first 3D printed house was created in China.
Since then, we’ve had our first experience with 3D printing in Hornet’s own business. One of our clients had a 3D sample printed for us to send to the Chinese manufacturer. Of course we specified materials and tolerances in the traditional way, but the ability to produce an exact sample of a complex shape is exciting. It makes it much easier to overcome the challenges of language and distance when prototyping and sourcing.
3D printing remains expensive – the raw materials used need to be very high quality. It’s also too slow for volume production. However, it’s ideal for rapid prototyping and product innovation. Especially when designs can be electronically transferred and printed out locally within 24 hours. This cuts out the delays and hassle of sending samples back and forth.
Hornet Verdict:
3D printing offers opportunities to prototype and sample faster, with lower costs and better quality. It’s also fantastic for small-run, one-off or personalised products. But it’s not at a stage where it can compete with traditional methods of volume mass production. That’s still many years away.
Overall, this is a manufacturing trend we like.
2. Use of Industrial Robots and Automation
Machines have been helping humans make things since the Industrial Revolution or even earlier. The word ‘robot’ was coined in 1920 and comes from the Czech word for ‘forced labour’. It tends to make us think of human-looking ‘androids’, but most robots currently in use are not humanoid at all.
The top 5 countries for industrial robots employed over a million of them by the end of 2014 – and were adding over 150,000 a year.
Automation is highest in the automotive industry, which is one reason the car manufacturing nations of South Korea, Japan and Germany have a high number of industrial robots compared to workers.
China’s automotive sector is at the same level with 281 robots per 10,000 workers, but minimal automation in other sectors pulls the national average down. That may not stay the case for long. 20% of all new industrial robots in 2013 were in China. It’s part of the country’s push to higher value, more sophisticated manufacturing.
And what about Australia?
Around 700 industrial robots are imported each year. The loss of local automotive manufacture may affect that figure. In other sectors, one high profile robotics implementation is by Patrick Stevedores. Driverless robots are replacing workers handling cargo at Botany Bay.
Hornet Verdict:
The manufacturing trend to robotics and automation is driven by the need to improve productivity. Australian manufacturers who want to compete globally will need to look into this area. Even if it means loss of some jobs.
3. On-Shoring, Re-Shoring and Next-Shoring
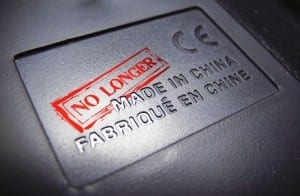
Is China losing manufacturing dominance?
Probably the most talked about international manufacturing trend of 2014 has been ‘re-shoring’. Rising costs in China have made manufacturing there less cost-effective. Local and near-local manufacturing, close to markets, has always been attractive as short supply chains mean faster response to changes in customer demand. Now it has become financially viable again. Manufacturing in the US, Mexico and the UK has been booming. The US has also benefited from lower energy input costs due to shale oil production.
So China may face challenges from the re-shoring trend, but it’s not helping Australia. Local manufacturing costs remain shockingly high, nor are we near major markets.
Hornet verdict:
A lot of sound and fury about this one, but not that much impact for the average Australian manufacturer. There is some possible advantage from factories in China being more flexible due to lower demand from Europe and America, but it’s not a major factor.
For low-tech goods like textiles and clothing, it may be worth exploring other low-wage Asian countries as well as China. Hornet already handles some projects from India, although we don’t have our own office there – yet!
4. The Internet of Things
The internet is about connection. To date, it has largely connected humans with other humans. Most computers, smartphones and other devices on the internet have a human being behind them controlling the interaction. But that’s starting to change. More and more, the internet is also connecting humans to automated devices (‘things’) – or even connecting things to other things. Early uses include remote monitoring – think snowcams and surfcams, or home security systems, or systems which track where your bus is and how long you can expect to wait. Increasingly, the connected ‘things’ are doing more than simple monitoring. What about the ability to turn your air-conditioning on before you get home? Or switch off timed sprinkling of the garden when it rains?
Those are consumer examples, but what does the Internet of Things mean for manufacturing? There are two main areas to consider:
Within the manufacturing environment
More sensors, monitoring more details of the production process, can manage production better. Maybe you can track quality measures real-time rather than after production. So you fix quality issues earlier, with less waster. Or you get indications when preventive maintenance should be carried out. So you reduce unscheduled, expensive downtime.
In relation to the ‘connected product’
When a product feeds information about how it used back to the manufacturer or designer, there’s more information available to improve the product. That might mean quicker product improvement and redesign. Or it could mean adjusting which products to manufacture based on real-time information about what consumers have bought and activated.
While the opportunities seem huge, so are the risks and challenges:
- how will we manage this increased complexity? What interface will we use?
- with more monitors and sensors sending information to various parties, what are the privacy implications?
- what about security? For commercial applications, this may include protecting intellectual privacy
- the environmental impact of millions of devices connected via semi-conductor chips may be huge.
This Australian Financial Review article gives an Australian perspective on the Internet of Things and how it may play out in the future.
Hornet Verdict:
This could be the biggest trend of them all, but it’s too early to predict what the impact will be.
5. The China Australia FTA
It’s less than a month since agreement about the China Australia FTA was announced. It’s worth remembering that no FTA has been signed as yet, nor has an implementation date been set. All the same, the expectation is clearly for lower tariffs between China and Australia.
For Australian manufacturers, there’s likely to be increased price competition from importers. Maybe it’s time to use the Internet of Things to improve productivity and control costs? Or maybe some components can be sourced internationally at lower cost?
We also found an interesting article on a US site suggesting Australian manufacturers could import components tariff-free, then manufacture and re-export to the US market.
Hornet Verdict:
Australian manufacturers will need to review operations and explore new ways to compete. There are opportunities, but new thinking and radical change are required.
Sources:
http://www.industryweek.com/technology/5-manufacturing-trends-will-shape-market-2015
http://www.automationworld.com/manufacturing-trends-2015
http://www.plantengineering.com/single-article/ame-mmi-releases-manufacturing-trends-for-2014-2015/5a585e7f4502f73790d5e4997a20a5a9.html
http://www.manufacturingglobal.com/technology/222/Manufacturing-tech-trends-shaping-the-industry-in-2015
http://www.worldrobotics.org/