Whether you’re manufacturing in China or in Australia, you may want to consider sourcing your moulds from China. A number of factors mean it’s possible to save many thousands of dollars.
- There are hundreds if not thousands of potential mould makers, so competition is fierce. In Australia mould making is a specialist business in itself, but in China many factories are accustomed to making their own moulds. They are equally happy to make one for you, which is why there is so much competition. (Of course quality control is vital, but we’ll come to that later.)
- With relatively low labour costs, labour-intensive processes like machining and surface finishing are far cheaper.
- There is a good range of materials to make moulds from. So it’s possible to match your mould material to your needs.
Even at China prices, a mould is an expensive item, so it’s worth following a careful process to ensure you get what you want. Many of Hornet’s custom manufacturing projects have required moulds to be made, so we’re well aware of these key issues.
Considerations when Sourcing Moulds from China
Mould specification
There are two main options when it comes to specifying a mould.
- You specify the mould you require in detail. This includes drawings, electronic files and precise measurements. Be sure to highlight any critical measurement points, plus what tolerance you will accept.
- You provide designs or samples of the item the mould will produce. The supplier then designs a mould to create these pieces. They have the freedom to determine where the mould splits, where the entry gates for injection are located and so on.
Unless you have experience designing moulds, the second method is probably easier. But remember that many injected materials shrink after removal from the mould. If the supplier is designing the mould, they need to account for that. Shrinkage rates are different for different materials, so make sure you specify what material you will be using with the mould too.
CNC Samples
CNC (Computer Numerical Control) samples are precision-milled from a low-cost material, to the shape the mould will eventually produce. As you can see from the photos below, a physical CNC sample is a great way to ensure the proposed mould shape is fit for purpose.
The left hand photo shows the CNC sample including:
- a square hole for switch to project (and connect with other components to turn on and off)
- a round hole allowing bulb to project (far enough for visibility but still protected from damage)
- internal protrusions (four in corners of left part, one in centre of right part) to hold the switch-and-bulb-assembly securely in place.
The right hand photo shows a piece produced (in higher quality materials) using the final mould.
(By the way, our client for this project achieved a cost saving of over 80% compared to an Australian-sourced mould!)
What Material to use for the Mould
Generally speaking, the higher your production volume, the better quality material you need for your mould. That increases the price.
If you’re a start-up or if you’re launching a new product and don’t know volumes with certainty, consider aluminium or low grade steel for your first mould. You only need a few thousand shots to test the market. If you’re successful, you can justify a more expensive mould for further production. If the product doesn’t take off as expected, you’re not as far out of pocket.
If you want a few hundred thousand shots from the mould, you need a low to medium grade steel as the mould material.
For the highest volume products, really high quality steel is required.
In Hornet’s experience, mould manufacturers in Australia tend to offer high quality moulds made from premium materials. These are fantastic for high volumes, but what if your production levels are not that high? You won’t have quality problems, but you may have spent some thousands more than you needed to on your mould. The smaller the production run, the higher the mould cost per item, and the harder it is to compete.
Payment Terms
Hornet never recommends paying the full cost of any project upfront. This is even more important for moulds. Ideally, pay 30% as a deposit, then pay the remainder of the mould fee when you are satisfied.
Mould Production Time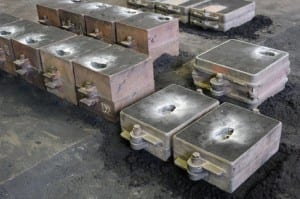
How long it takes to make a mould depends on its size and complexity. There are technical considerations around the core and cavity; the injection system and the cooling system. Complex shapes may require additional sections to the mould, all of which add to cost and time. Most moulds are rough-shaped by milling, then hand-finished using one or more processes. This could be grinding, texturing, sand blasting or even hand polishing.
It is always worth allowing more time than you think will be needed for production of moulds from China. While adjustment and modification is not always required, it is not uncommon. Better to have extra time to sort out issues rather than not enough!
Quality Considerations
Examine samples produced using the mould.
- Is the shape correct?
- Is the size correct?
- Are there obvious gate marks or parting lines? (where the polymer was injected, or where the parts of the mould are clamped together?
- Is the surface texture acceptable?
You may want to check the material used in the mould, especially if you are planning a large volume of product.
Contractual terms can also be a good quality tool. If you’re importing the mould to Australia, or using it in a different factory in China, have a clause with penalties if the mould fails before a certain number of shots. If the mould is going to be used by the same factory which made it, your risk is lower. The factory has an incentive to create a good mould, so they can make good product for you and get paid for it.
Ownership and Use of Moulds in China
If your mould will stay in China and be used there, think about what happens to it between production runs.
- Where is it stored?
- Will it be protected from rust and contamination?
- Will the factory be tempted to use your mould for other customers and export similar product? You may want a clause into your contract to prevent this.
Or you can have the mould moved to a third party for storage and safekeeping. Dependent on the size of your mould and the location of the supplier, Hornet may be able to store your mould at our own warehouses in China.
***
Sourcing moulds from China requires some investment of time and care, but in return it can cut significant cost from your supply chain. If you’d like to explore this idea further, why not contact Hornet for a no obligation discussion?